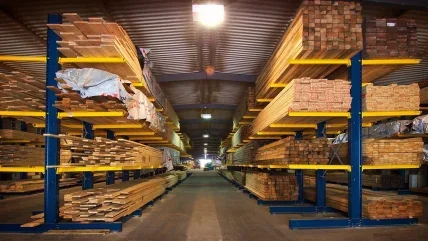
Founded in 1966, States Industries LLC is a leader in hardwood plywood manufacturing, supplying environmentally conscious, premium hardwood panel products to North American woodworkers.
States was the first in the industry to be FSC-certified, to introduce pre-finished plywood and convert to using soy-based adhesives in all of its panel products.
The company is formed by more than 300 employees and two different facilities. The primary mill site is located in Eugene, Oregon, and it also operates from DrawerBox DBS, its brand for drawers, storage products for cabinets, in Orange, California.
With a passion for innovation, States Industries says it is committed to world-class manufacturing and is constantly looking for ways to improve products, support the changing demands of the industry and manufacture custom hardwood plywood for craftsmen, architects, and designers.
THE CHALLENGE
As part of an expansion and growth plan, States Industries was immersed in a process of upgrading and improving the production facilities. Thus, this growth strategy included a project for a new hardwood plywood panel press line, for which a large investment was necessary.
This investment was a strategic move by the company.
The objectives were production capacity increase for high value panels, and the improvement of manufacturing product quality from a wide array of panel sizes, substrates, hardwood veneers, and order quantities.
According to States Industries vicepresident of manufacturing, Ted Downs, the deployment of capital toward manufacturing higher value hardwood plywood was well timed for the demand the company had been experiencing in the market.
The main challenge of this project lay in developing a hardwood veneer press line that would enable States Industries to produce almost fully automatically what it had been always producing in a manual way.
THE PROJECT
The solution consisted of an automatic line to produce hardwood plywood panels, up to 10ft in length, through a short cycle multiopening press. International technology specialist Biele partnered with States on the project.
The project involves a fully automatic handling and cleaning of the substrate, gluing on top and bottom surfaces, and semi-automatic lay-up of top and bottom hardwood veneers that then feeds the fouropening press.
This happens in a non-stop basis using a four-basket infeed and outfeed system. Regarding the press, it operates with 514 Tm pressure and 130°C temperature, resulting in a capacity to produce four boards/min.
Behind the press, the line is also cleaning the overhanging veneer of the panels without any trimming of the substrate and includes a vertical putty section in case panels need to be repaired before stacking. All these processes are completed continuously without any stops.
By means of a customised design of the system, Biele accommodated the required process in the available floor space, adapting to customer’s needs.
THE RESULTS
Essentially, what the press line allowed States to do, is to produce panels with much better labour efficiency. In this sense, the press line allowed States to reallocate about 14 people from areas where they were producing panels in their conventional old way, into other areas where they can grow more value. As a consequence, in the last year States has grown its production capacity by at least 30% with far fewer people involved in making the process.
Additionally, the press line allowed them to cut their reject rate by about half.
“This put us in a very favourable position in terms of recovering that value out of the panel,” said Mr Downs.
Moreover, because the press is a 4-opening press, it allows States to do smaller quantities much more effectively and much easier than its conventional 30-opening presses that tend to get dirty and have other issues around when they are running on other types of products or producing small quantities.
“Thanks to this new press line performance, we managed to gain more market share, and achieved a more efficient production with much lower fall down rates,” added Mr Downs.
“Incidentally, one of the great outcomes of this, is that because we have a lower fall down, and because we can do special order or exact order quantities, it reduces the overages that we produce in the inventory, which, of course, helps with our financial positioning as well”.
THE EXPERIENCE
This hardwood plywood panel production line has been the first project collaborations developed by Biele for States Industries LLC.
“We have delivered an innovative hardwood veneer press line as a result of a close teamwork between our technical teams and a clear vision from States Industries that led to a successful partnership,” said Biele USA general manager Juan Flores.
“We’ve been able to produce significantly more three-ply and two-step production at a much lower falldown rate than through our conventional vertical multi-opening presses,” added Mr Downs. “Biele’s automation simply brought us better efficiency and recovery of grade, which we’ve been able to reinvest into our people and additional automation.
“One of the things that was a challenge for Biele as well as for States during the project, was that the pandemic occurred, and it became very difficult for communications and travel back and forth between Europe and Oregon. In this sense, one of the things that Biele did very well for us was that it never abandoned us during the project.”
“Biele modified, it adapted its schedules, it adapted its staffing, to try and help us accomplish commissioning the line on time. With the pandemic, of course, things were delayed, but we were able to commission the line really close to the projected timeline that we had envisaged during the initial project stages.”