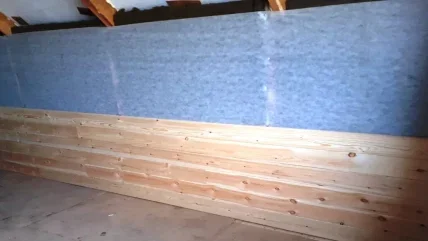
Wood panel manufacture is a fascinating thing. On the one hand it is such a simple concept. Take the wood particles (or fibres, or strands, or veneers) and take some glue, combine them, press them and you have a new material. Talking to new students, or school kids, or the public this might be as far as we take the story. Perhaps we talk about aligning the strands in a specific way, or using a certain adhesive to achieve the best properties.
But if you dig deeper, and start to lead students on the journey into what is happening in the press, you touch on lots of concepts. The role of steam in transfer of heat, or the way the particles soften in this high temperature / high moisture environment, or the way the resin gels first then cures into a much more rigid state.
At this point we can reach for textbooks and graphs, or whiteboard markers and scribbles. We try to communicate things we can’t see, but can sense. We start to lean on understanding gained from lots of different experimental work, using different sensors, locating them in test boards and ‘watching’ the data to see (or understand) what is happening.
Take the simple temperature and vapour pressure probe. In experimental work, with new furnishes, new adhesives or new additives this is indispensable. Sensing temperature in the core of the board is essential to know that the cure conditions have been met. This is simple, a normal thermocouple could do this. On the basis of a thermocouple you could watch the core temperature rise, maybe locate extra thermocouples in the surface region and see the difference in real time.
But if you couple this temperature sensor with a sensor that can detect the vapour pressure you unlock the other side of the story. The moisture in the surface regions of the mattress is heated and migrates (as best it can) towards the core. This is a shorter distance than the route to the edge of the mattress and the open air. This movement of steam takes heat towards the cooler core material and starts the thermal processes here. The vapour pressure in the core of the panel can become very high in the time before the steam manages to migrate laterally to the edge of the press.
Knowing how high this vapour pressure gets can be very helpful indeed. In panels with exceptionally high moisture content, opening the press too soon will lead to blows, sometimes with explosive results. I once worked with a binder that had an unusual moisture content, and the vapour pressure led to the panel attempting to exit the press like a frisbee! Thanks goodness for safety screens in the lab set up. Normally the blow or delamination happens more predictably, the core of the panel pulls apart and a crispy surfaced sandwich with a slightly hollow core is emitted from the press.
If the vapour pressure is known, then the due adjustments to furnish moisture content can be made, or more often the press profile adjusted to change this build-up of pressure or to hold the press closed until more steam has managed to exit the panel edges.
Such a simple piece of equipment, but such a large extra piece of knowledge for panel development. As for the art of placing the probe in the dead centre of the mattress every time – now that requires skill of a different kind. Only experience can give that extra sense to the operator.