The whole line is to be assembled and tested at Vits before delivery to the customer. This is not just a new impregnation line, but one which runs at speeds never before achieved. "The new line will run at up to 120 metres a minute for certain melamine products," said head of sales for plant engineering Daniel James. "Current impregnation lines available on the market are limited to around 60 metres a minute and we expect this one ultimately to run at a steady speed of 100 metres a minute." Mr James went on to explain the development route which the company has followed to reach this stage. "We looked at all the bottlenecks on existing lines and talked to our customers who were running at the fastest speeds. A lot of research and development went into this new line and this is the most modern equipment in the world today," he said proudly.
The line includes a brand new impregnation unit to suit the customer’s requirements. It will be delivered in early 2007. Mr James said the new sheeter was one of the crucial developments; with a line running at those kind of speeds, and the fragility of decor paper, rapid and careful handling of the treated paper at the end of the line was obviously going to be important. "This involved a lot of development in terms of ease of maintenance, the drive system and an ‘active’ stacking system that takes the sheets of treated dried paper away, rather than just dropping them onto a pallet in the conventional way," said Mr James. Three on-the-line measuring heads for the raw paper, intermediate stage and the final product, developed jointly with Scienta of Finland, have been integrated into the Vits control systems and intelligent software which will operate the line. These will provide a wealth of information to the operator, said Mr James.
"It is not just the usual weight and moisture measurement, but other parameters such as temperature, degree of polymerisation in the dryer and other factors which will enable us to get the maximum possible out of the length of the brand new design low-energy dryer. We can measure all we need to know for this," he explained. There are also more scanners in the cooling area after the first dryer and before the second, plus a gravure unit for the intermediate melamine coating. Of course a faster line speed requires faster drying – hence the development of the dryer. The sheeter has already been successfully tested with standard decor paper at 120m per minute in various widths. The new line is expected to be available to the general market in mid-2007. In the meantime, Mr James said that Vits has a full order book. One of those lines was for a Russian panel making factory and another under assembly for Russia was for a filter paper coater for the automotive industry. Sheeters for offset printing lines are another good source of business for Vits.
The panel industry today accounts for about 70% of the company’s turnover. "We are also the only manufacturer of impregnation lines which can offer our lines certificated to the ATEX 100 explosion safety regulations," claimed Mr James. A lot of Vits’ component manufacturing is sub-contracted to specialist engineering firms who have a long history of supplying the company’s requirements. The sheet metal components come from one of three suppliers in northern Germany, eastern Germany and the Czech Republic. "Which supplier we use depends on where the final machine is to be delivered," explained the sales manager. Vits also has a joint-venture company in China. Vits Imaco (Suzhou) Engineering Co Ltd was established in a 10,000m2 factory in 2004 to supply the Chinese and South East Asian markets with impregnation lines with around 80% local content. A new factory hall to make products for the printed circuit board market is planned there.
Precision components such as the rolls for the impregnation lines are carefully checked at the Langenfeld factory on arrival before being fitted with the high-precision bearings and then being assembled into coaters in the assembly area. These bearings are set to very tight tolerances and are adjusted on a special granite base. Vits does not work alone in developing its lines. "We have a lot of customer visits and we work very closely with our customers on R&D. We also have a much closer relationship with the paper makers, printers and resin suppliers than we did in the past," said managing director Achim Hackspiel. "Flooring is a classic example where, when they were looking for an abrasion-resistant surface, we worked with the resin, paper and corundum suppliers to develop the successful ARP (Abrasive Resistant Pre-Impregnated Products) system."
Registered embossing of papers, in which the embossing matches the printed woodgrain detail for example, has also required the same cooperation to achieve a treated paper with the right physical characteristics, particularly with regard to stretching. The Vits company was bought by entrepreneur Werner Deuring in 2002 and in April 2006, he sold a majority shareholding to Granville Baird, a UK-based investment firm. This has freed up capital for further investment in R&D. The company has a new structure, with Vits Group, Langenfeld, at the top of the family tree. Vits Systems employs around 150 people. IFA in Bavaria specialises in resin mixing systems and has 25 people. Vits Imaco employs around 130.
In 2005, Vits developed a finish foil line for pre-impregnated paper, printed and coated in the line and wound on reels. This was for Süddekor of Germany and included making the printing head. It runs at up to 300m/minute. A second line, for Interprint of Poland and with a speed of 200m per minute, was due for delivery in December. "This year has been very good for us in our traditional lines too," said Mr James. "Turkey has been very active as has Russia and we feel that North America is about to improve as a market – we have supplied several lines there recently and see an increasing demand. Three lines were also sold to South East Asia in 2006. When it comes to new developments in the race for higher speed production, Vits Systems would currently appear to have a firm hold on the baton.
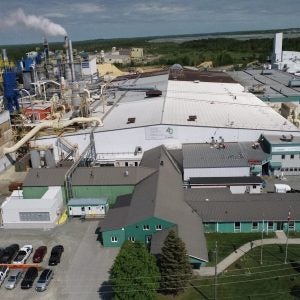