The target market covers a broad spectrum from large publicly- and European Community-funded projects to work for commercial enterprises. "It is paramount to us to have a broad range of projects and not to have all our eggs in one basket to mitigate the financial risks – no one project accounts for more than 20% of our annual income," said Dr Fowler. "That exposes us to a wide variety of industry sectors and develops our knowledge base as well." Rob Elias is the commercial manager of the BioComposites Centre and its main initial point of contact with the industry. "We do not carry out ‘blue sky’ research by which I mean research for its own sake," he said. It is important for us to work with the industry and to understand their needs and to feed that information back into applied research.
"We carry out ‘technology scouting’, keeping up to date with scientific literature and our colleagues [academics] and looking at how to apply that information in a commercial situation; translating that knowledge into projects which fulfil an industry need." The forest products sector is a key part of the centre’s work and in that sector issues of sustainability are very important today, said Dr Elias. "The built environment is a key area on which people are focusing and this provides market opportunities for technology transfer in the areas of adding value, reducing production costs and developing new research programmes." As an example from the solid wood industry, Dr Elias quotes the use of CCA and creosote preservatives where the centre has been looking at natural alternatives as a direct result of legislation in this area. "We also need to look to the future and see where the next generation of legislative pressures on the industry might come from such as minimisation of waste, end-of-life recycling, contamination and so on," added Dr Fowler. "For example, if you burn MDF what emissions will there be?"
Public clients for the BioComposites Centre include UK government departments such as the Department for the Environment, Food and Rural Affairs (DEFRA), Department for Trade & Industry (DTI) and government-funded initiatives such as WRAP, which is charged with issues surrounding recycling. There are also EU-funded projects in areas such as emissions, recycling and sustainability. The EU’s COST Action E49 for the science-based advance of panels and their production processes is an example of this (WBPI issue 6, 2005, p51), as is the Forest Based Technology Platform. Commercial clients are all in the renewable/sustainable materials industry from fine chemicals to the wood products industry and this was summarised by Dr Elias as: "Any industry where there is a desire or requirement to reduce the environmental impact of their operations".
At any given time, the centre is running a project for at least one wood based panel manufacturer, normally concerned with solving a problem experienced within its own operations. "Most of our development work – and our expertise – in the panel sector is with suppliers to the mills, such as resin and additive manufacturers," said the commercial manager. Companies producing resins and additives for use in panels and other wood products are also well-represented on the client list, including non industry specific chemical producers who want a product evaluated to see if it could be beneficial to the forest products sector. Agricultural fibre based panels are a major area of work too. However, there are occasions when the BioComposites Centre will initiate a project. "If we have an idea we will go out and seek a potential commercial partner, for example for new rapid test methods. Our current project concerns waste recycling technology for MDF and we are negotiating with a capital investment company to bring this patented process to market," said Dr Elias.
"We also have a patented process for bioresins based on rape seed oil, which we are trying to commercialise. The waste material from the process can be used to fire the process, thus ‘closing the loop’ environmentally." The University of Wales, Bangor is currently going through a major restructuring process, in line with new government policies for higher education in the UK, and part of that reorganisation has involved redevelopment of the university’s buildings. As a result, the BioComposites Centre lost its original premises, currently under redevelopment to become The Environmental Centre for Wales, and moved into a floor of the 10-storey chemistry block next door. At least, it moved its offices and laboratories next door, but there was no room for the 15-year-old MDF pilot line. "That was decision time," said Dr Fowler. "Should we scrap the line or invest in it to make it viable for the next 10 to 15 years or so?" It was decided to take the latter course and, with infrastructure funding from the devolved Welsh Assembly government, the EU and some of its own resources, BioComposites found premises at Mona on the neighbouring Isle of Anglesey, 15 minutes drive from the University, to accommodate its MDF pilot line.
The premises comprise three light industrial buildings which have now been inter-connected so that the pilot line with its improved dryer system, one hot press line with Pressman controls and steam injection capability and a small laboratory facility can be accommodated. Compression moulding of shaped profiles such as chair backs will also be possible. Meanwhile, back at the university, BioComposites has its research laboratories on the sixth floor and a rotary blender, laboratory press, wet former for wet-process fibreboard, shives analyser, density profile meter, atmospheric refiner and dry kiln in the basement of the adjacent building. The laboratories have also received considerable investment. The analytical facility has chromatography for characterisation of resins and analysis of small amounts of materials and an infra-red spectrophotometer with optical microscope to study individual fibres to check resination, for example. In the resin/chemical development room is Dr Fowler’s brand new pride and joy – a 50-litre reactor for resin production. There is also an autoclave for resin development and a Kajaani fibre length analyser.
In the resin and additive manufacturing laboratory is the centre of bioresin research – an important area of work. This lab features an ozone generator essential in the process of converting oil to resin and a reaction calorimeter. Both items of equipment are rare, said Dr Fowler proudly. The materials testing laboratory offers a range of equipment for testing the physical properties of panels, including an automatic bond analyser developed at the university. In addition to its own range of equipment, BioComposites is also able to rent time on some very sophisticated kit within the university, such as the spectroscope. In 1997, the then director of Bio- Composites held the first European Panel Products Symposium (EPPS) in Llandudno, just down the coast from Bangor. "Dr Bolton recognised a need to improve the technical understanding of the industry and to provide an opportunity for technical managers to hear what is going on in scientific research relevant to the future of the panel industry and that is the philosophy which we have retained with EPPS ever since," said Dr Elias.
This annual event will celebrate its 10th anniversary in style on October 10-13 this year. In addition to the usual programme of scientific, technical and industry-relevant papers being presented at the symposium, the organisers promise a visit to the new technology centre on Anglesey and a very special gala evening at Beaumaris Castle, a World Heritage Site. "The symposium is a mixture of the academic and the applied, just like the Bio-Composites Centre itself," said Dr Fowler. There are also significant plans to move the symposium on to a new level and these will be announced at this year’s event, he added tantalisingly. Summarising BioComposites philosophy, Dr Fowler said: "Our key competence is innovation – we help companies such as resin producers and panel manufacturers to innovate in terms of their products and processes, to save money, develop new markets or improve the properties of their existing products and processes. It’s about innovation, sustainability, making things cheaper, cleaner, better".
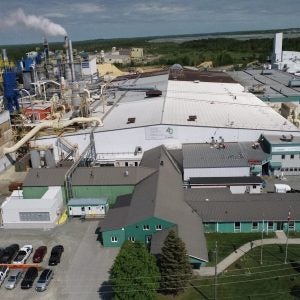