The dryer plant has a combustion chamber with a special geometric design for purification of silica dust particles and control of the internal temperature, created with regulating shutters, which prevents the silica melting. The plant is also equipped with a continuous silica extraction system, for both vertical and horizontal chambers.
"This system, as per our expectations, has contributed noticeably to reducing the wear on the plant, thus drastically reducing the time for which the line must be stopped for repairs," says Mr Stocco. He also says the optimised combustion system, with the air being measured by a Venturi tube, and the perfect dosing of the fine powder by the Instalmec bunker and rotary valves, have over time proved to be a guarantee of reliability and performance, evidenced by savings in both costs and energy.
"The Omega pre-drying system has proved to be highly efficient in the drying process as well as in gravimetric separation, the latter function being greatly appreciated in a plant which treats recycled materials." The large drum of this dryer came with what Mr Stocco refers to as "innovative solutions" in terms of the internal parts. He claims the result is in line with expectations and has optimised the drying of both fine and coarse materials. Furthermore, he says, the separation downstream of the drum has guaranteed the hoped-for increase (about 50% more than traditional systems) with minor stress for the cyclone battery and related pipes. The new dimensioning of those pipes was designed to reduce wear to minimal levels. "The heart of the plant, the fan, was created using innovative materials and technologies and thanks to the fact that material does not pass through it, it has a practically unlimited lifetime," says Mr Stocco. "All this innovative technology has permitted a saving in absorbed Kilowatts equal to 40% compared to traditional types of drying systems. The plant is easy to operate thanks to a clear, user-friendly videographic system." Following the successful inauguration of the new drying system, Annovati signed an agreement with Instalmec to resolve another complex issue: cleaning the dried material. This area of the plant had always been considered a ‘danger area’ due to the high level of flammability of the dried wood; the detection systems for spark detection/fire extinguishing are always in action.
This meant it was necessary to propose new, reliable, equipment to resolve these problems. "Instalmec has years of experience in separating contaminated materials with its range of gravimetric separators, and its philosophy has always been to create made-to-measure equipment for Annovati. "The introduction of this equipment into the lay-out of the system has been studied down to the smallest detail with the aim of achieving excellent functionality and reducing installation times. "In fact, during the August break in 2005 it was possible to carry out this insertion and the results were immediately tangible," says Mr Stocco, adding that the detection and extinguishing systems no longer cut in and the Annovati technicians and operators themselves have now declared that the area is ‘forgotten’ and safe.
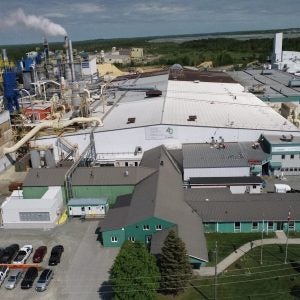