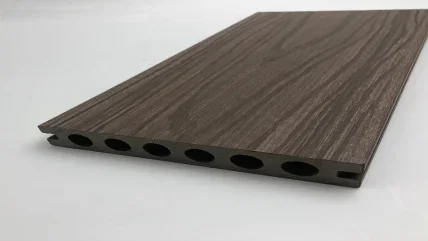
WBPI: CAN YOU EXPLAIN HOW THE EU HAS RESTRICTED THE USE OF DIISOCYANATES?
Erik Vangronsveld: As with other chemicals and the other main resins used in composite wood products, methylene diphenyl diisocyanate (MDI) – the core building block for polyurethane – has its own regulatory challenges. There are three key challenges that have been initiated over the last 10 years and that still are active/relevant in one way or another. However, it is important to stress that MDI can be used in the composite wood products (CWP) industry with limited impact from regulatory initiatives.
Challenge #1: 4.4’ MDI and mixed isomers (2,4’ & 4,4’MDI mixture) underwent an evaluation under the Community Rolling Action Plan (CoRAP) between 2013 and 2019. CoRAP evaluations can lead to a range of regulatory actions ranging from no action to authorisation – meaning phasing out over time.
The evaluation sought to clarify potential concerns surrounding MDI and its impact on human health and environment. In December 2018, after a long and in-depth assessment process, the European Chemicals Agency (ECHA) concluded that there are no immediate concerns for these two substances and that no regulatory measures are required.
Huntsman played a key role by leading the industry consortium that collaborated intensively with Estonia, the EU evaluating member states, by providing responses to the many challenging questions raised during the evaluation. Today, Huntsman is continuing to lead the industry to obtain the same outcome for all MDI registered substances (about 20) in collaboration with ECHA directly via a CEFIC (European Chemical Industry Council) pilot project. This process will take many years and a significant amount of new data needs to be generated, but we are confident that the same outcome will be obtained as for the initial two substances.
Challenge #2: On February 24, 2022, a new regulation on the labelling of diisocyanates came into force. To ensure the control of the dermal and inhalation exposure of industrial and professional users to diisocyanates in the workplace, all packaging must now mention that mandatory training will be required for all industrial and professional users of the substance as of August 24, 2023.
Again, Huntsman has played a vital role in advocacy around this change, including the development of training materials in collaboration with many downstream associations, including EPF (European Wood Panel Federation) under the ISOPA (EU association of MDI and polyol manufacturers) umbrella. ISOPA has developed an on-line platform (Safe use of Diisocyanates – Home EN (safeusediisocyanates.eu) where workers can obtain a training certificate to demonstrate compliance with this new training requirement.
Training is already available in multiple languages now, but all languages are planned to be available by the end of the year. This new mandatory training requirement should have limited impact to existing CWP manufacturers, as in this industry Huntsman has set a standard that regular MDI safe handling requirement is a must for every plant that is using MDI as a resin to produce CWP since the introduction of MDI in this industry in the 70s.
Challenge #3: In March 2019, the European Commission asked the ECHA to investigate how and to what extent the Occupational Exposure Limit (OEL) for MDI can be lowered to reduce the risk of occupational asthma cases. Having unique industry expertise in industrial hygiene, Huntsman played a key role in supporting ISOPA in its advocacy efforts to provide information on existing potential exposures, methodology to assess exposure and specific potential exposure risk and current risk management measures during the different PU manufacturing processes, including CWP manufacturing. Huntsman reached out to EPF to collaborate on providing this information to the consultant mandated by the EU Commission to come forward with an OEL proposal. The OEL being proposed, and which is now subject to discussion between the different EU Commission departments and still requires approval by the European Parliament and Council, should have limited to no impact to existing CWP manufacturing based on the available average exposure levels that have been measured over the last 25 years by Huntsman at the many different CWP manufacturing plants across the EU in support of their customers.
With the Chemical Strategy for Sustainability under the European Green Deal, there are possible new challenges ahead for MDI. Huntsman has a Green Deal team that continuously monitors and analyses anything that comes out of this EU initiative and that could affect the sectors that the company serves. This team assesses the possible impacts and decides the course of any internal and external actions together with the industry’s ISOPA team. The biggest potential red flag is that respiratory sensitisers have been mentioned as a hazard class that the EU wants to address. Huntsman believes this work will be more focused on consumer and professional uses and not applications at industry level, such as the production of composite wood products.
WBPI: CAN YOU EXPLAIN THE NEW LABELLING AND TRAINING REQUIREMENTS AND WHAT THEY MEAN FOR THE WOOD-BASED PANELS SECTOR?
The restriction prescribes mandatory labelling for products that contain >0.1% diisocyanates by February 24, 2022 and that workers are trained by August 24, 2023. The process for this restriction started in 2013 when Germany began an authorisation for TDI. Through very intensive collaboration and industry advocacy this has been turned around to the restriction that we know today, and which is applicable for all diisocyanates. ISOPA/ALIPA has led this project – working with more than 20 downstream associations, including the European Panel Federation (EPF), to turn this into a workable restriction. Huntsman was part of the initial advocacy team involved in this project and played an active role in shaping the restriction. Huntsman also played a leading role in the development of different training materials for the different MDI applications in collaboration with downstream users. We also organised webinars, hosted by our product steward, Liesbeth Melis. Each member state will have to report to Europe on an annual basis if, and to what extent, compliance is happening and the impact on occupational asthma cases over time.
WHAT TRAINING WILL BE REQUIRED (VIA ISOPA) AND WHAT CHALLENGES DOES HUNTSMAN SEE IN ITS IMPLEMENTATION?
The training consists of a basic training for everybody to follow and a specific application-oriented training to improve safe behaviour during the application specific activities, including composite wood manufacturing.
Training in best practice handling techniques for MDI is already standard in the composite wood products sector. Nevertheless, the need to formalise training for between four to five million workers is a big undertaking. To support diisocyanate downstream industries and facilitate the compliance of so many workers with the restriction, ISOPA has established an online platform where there are different options for training workers from online courses to face-to-face sessions.
For MDI use in the composite wood industry, the “Wood Composite Products” section includes basic training and CWP specific training. For loading / unloading at room temperature and for laboratory staff, only basic training is mandatory.
The different user options on the ISOPA platform include:
- Training as an individual;
- Becoming a trainer (certified trainers will be listed in the platform / Huntsman will develop a pool of certified trainers);
- Setting up an admin account to manage the training of staff.
WHAT ELSE HAS HUNTSMAN BEEN DOING ON THIS TOPIC TO HELP CUSTOMERS?
At Huntsman we continuously explore innovative technologies to improve board quality and production efficiency. In parallel, we are committed to supporting the industry through our well-recognised product stewardship work.
As a business, we are unswerving in the support we provide to the wood-based panel industry and want companies in this sector to work safely with MDI resins. To enable this we:
- Provide safety and product stewardship expertise including training / advice on the safe handling of MDI;
- Have unique industrial hygiene expertise in Europe for workplace assessments;
- Partner with the EPF to support and collaborate on regulation challenges.
In addition, we have enhanced our innovative MDI-resin technologies. Our global dedicated wood team can advise on the most adequate MDI-based solution for different applications, enabling the manufacture of composite wood products in an effective and safe way. For example, using the right MDI, you can produce high quality panels with exterior properties which contain no added formaldehyde. They can also provide front line technical production assistance where needed.