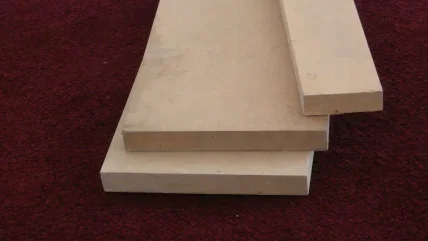
At the recent Ligna Digital Innovation Network event Dieffenbacher unveiled its Cebro smart plant concept.
Cebro, which takes its name from the latin word cerebrum which means “brain”, outlines four pillars – digitalisation, advanced plant engineering, sustainability and operational excellence.
Smart factories and Industry 4.0 are of course words we have grown used to over the last decade as new developments in technology and digitalisation have arisen to drive further production efficiencies.
It is the digitalisation pillar that we are focusing on here on this Focus on Germany article.
This specifically is the Evoris digital platform, which Dieffenbacher says has been garnering strong attention among its customers as the company seeks to fulfill the original Industry 4.0 concept on the path to the ultimate goal – the self-optimising plant.
It is the world of Artificial Intelligence, machine learning, interfaces, sensors and data analysis to produce smarter, increase production, reduce waste and predict and minimise the impact of production problems.
But before we look at this exciting area, let’s remind ourselves in more detail about Cebro’s core tenets.
Markus Trame, Dieffenbacher project manager marketing and PR, explains that the advanced plant engineering pillar outlines smart synergies in plants. Intelligent heat recovery concepts, such as reusing heat from the press and dryer exhaust air elsewhere in the production process, are just one idea to reduce energy costs and emissions and increase profits.
The operational excellence pillar uses optimized processes and innovative technologies to improve board quality, increase output, save costs and support sustainability.
Examples include new technologies recently introduced by Dieffenbacher such as a new particleboard forming station to improve board quality with increased spreading accuracy.
Others include the EVOsteam steam preheating system to enable higher production speed and capacity, while a new belt dryer and an emission management system are also new.
The other pillar is sustainability which helps manufacturers to reduce emissions and CO2 footprint, save energy, use recycled wood and reduce material consumption.
EVORIS DIGITAL PLATFORM
And so to Evoris, the digital pillar of Cebro, which has been created in-house by Dieffenbacher’s digitalisation team.
“We have developed a completely new approach in the digitalisation of wood-based panel production plants, using Artificial Intelligence (AI) and machine learning to support production operators and technologists so they can receive insights into production processes, helping to benefit from higher plant availability to reduce unplanned downtimes, to increase capacity and be able to save raw materials,” explained Axel Ganster, Dieffenbacher’s team leader wood technology.
“This is the aim of Evoris, to produce smarter. It is collecting and processing data throughout the entire plant and this data is fed to AI-based applications to turn in into easy to understand useful information.”
Evoris has three pillars –
- connectivity and transparency
- analysis and condition monitoring
- prediction and optimization
Mr Ganster said Evoris is a combination of the IBA system and Dieffenbacher’s Evoris start centre for applications. The IBA software, which collects all factory machine data into one single database, is the only non Dieffenbacher part – everything else from the apps to the algorithms and visualisations / design has been designed in-house.
The IBA system has been operating successfully for decades with over 20,000 installations at industrial plants worldwide, for example with customers in the steel and paper industries. The advantage of the IBA System is it can connect with any machine, irrespective of who supplied it.
It already has comprehensive connectors for many different types of machinery, which, says Florian Schleissinger, Dieffenbacher software and digitalisation AI expert, means it is a proven out-of-the-box technology so Dieffenbacher doesn’t have to reinvent the wheel.
Some wood-based panel producers have used IBA software for individual machines, he added, but it is not yet widely used in the industry.
That is about to change as Dieffenbacher has an exclusive co-operation with IBA to use the system in the wood-based panels industry.
“We are introducing it in the sector,” added Mr Ganster.
“From now on every plant Dieffenbacher delivers to our customers will be already equipped with the IBA system as standard. This will be the new gold standard for the wood-based panels industry. It is in widespread use across the globe with many installations in the paper industry which is close to the panels industry with similar production processes.”
The IBA software forms part of Evoris’ first pillar (Connectivity and transparency) – collecting data throughout the plant and storing it in a centralised database to make it available for reporting and other apps.
The second pillar – analysis and condition monitoring – consists of various tools, apps and sensors to be able to better understand processes, provide faster trouble shooting and to help to gain higher plant availabilities. Tools include the anomaly detection app.
In the third pillar – prediction and optimisation – apps include the Evoris quality prediction app, which is an AI-based self-learning system to help customers increase production output, reduce rejects and save resources.
Overarching these three pillars is the free service and support package to make a digitalisation solution as easy as possible for customers, comprising training and functional updates on a regular basis.
WEB-BASED SYSTEM
Evoris is a web-based system accessed on common browsers and operating on any computer or digital device, with no software to be installed.
It is multilingual and designed with an easy-to-use interface with optimisable dashboards.
You can choose the apps you want to put on the dashboard, change the size of charts/KPIs or go into detailed views. Users get informed of Evoris updates and receive warnings about production anomalies or quality issues so countermeasures can be taken.
Cameras are integrated in the production line, effectively synchronising live stream images with data signals coming from machine sensors.
“From a production and maintenance point of view it’s very important to have the video stream,” said Mr Ganster.
“If for example the control room operator arrives for the morning shift and sees there were stops in the night shifts you can see exactly what happened. Measuring and ‘seeing’ equals understanding.”
The Anomaly detection app is an important part of the system.
“We use AI / machine learning algorithms on the data to define what is normal for the production so we can then define in the live data if there are any anomalies,” said Mr Schleissinger.
A dial on the Evoris dashboard will display a figure for the optimum production and how live manufacturing may be deviating from that.
“Machine learning methods mean you don’t need to set different thresholds for different productions. For every production condition the algorithm automatically works out what’s normal and what constitutes an anomaly.”
Importantly, the system shows what signals are causing the anomaly to determine where the problem is – for example the surface layer pressure of the static mixer may be rising, indicating a glue nozzle blockage or pipe problem.
“If there’s a blockage of the glue nozzle this means you may have rejected boards due to bad gluing and you have to stop to clean the nozzles and then restart,” added Mr Ganster.
Having transparency and full visibility means it is possible to react quickly, without having to look at thousands of data points at the same time.
“A reduction of downtime and board reject numbers represents so much money in this business. Already small numbers are producing high savings here.”
QUALITY PREDICTION APP
One of the many apps available is the quality prediction app.
Mr Schleissinger explained that traditional lab analysis of samples – testing MOR, MOE, IB and surface soundness for example – takes several hours to have results.
“But with the quality prediction app we can deliver real time predictions on the production line. It is a fully self-learning AI system. We take the lab data and corresponding process value and do a supervised learning so the AI learns what quality results from the process values and by this we can make a prediction for the live process. The operator can then adjust production and is not dependent on waiting for the lab any more.
“The goal is always to produce closer to your quality limits. When you do this, you can save real money in respect to glue, wood and energy.”
Mr Ganster explained that data collection wasn’t difficult but the “real magic” was the algorithms and machine learning behind the apps, combined with Dieffenbacher’s automation and technological know-how and work with its customers and partners, including experts at the Fraunhofer Institute.
“To get this whole concept working, Dieffenbacher completely changed its development process, shifting from classic project management to an agile development process.
“We integrated all relevant parties into agile teams which makes development easier, faster and more flexible.
A 12-strong Dieffenbacher team worked on developing Evoris and further work is ongoing.
“Digitalisation – Industry 4.0 – will be the future so this is why Dieffenbacher is investing now,” added Mr Ganster.
“We are seeking the target of the self-optimising plant. You can only get to this ultimate goal when you know exactly what is going on in your production process. So, you need all the data to do this. The next steps are clear, we have to develop some offline simulations and the next future step will be the self-optimising plant.”
The Dieffenbacher digitalisation team is working on multiple projects, including additional Evoris apps, with various additional tools for analysis/condition monitoring to detect potential machinery defects and give you up-to-date conditions of machines to give operators the opportunity of preventative maintenance measures.
There are also new in-line sensors and a corresponding app planned to determine particle size. A prototype will be installed at a customer soon.
The technology uses AI and represents, says Dieffenbacher, an industry first in terms of in-line continuous particle measurement for either particleboard or OSB lines.
“We will not stop here, we have a very big backlog of ideas coming from our customers, partners and Dieffenbacher staff,” added Mr Ganster.
He said the future self-optimising plant doesn’t look as far in the future as it did at the last Ligna exhibition, with development work speeding up.
Feedback to Evoris and Cebro at the Ligna Digital Innovation Network was “very good”.
“We made many presentations and customers said Industry 4.0 was becoming more visible now. They told us this was exactly what the industry needed and everyone wants to discuss this – either for retrofit or with new plants.”
Swiss Krono Group is the first panels producer to use Evoris.
Finally, to answer any concerns about data security, Dieffenbacher developed the system based on ‘edge’, which means all data is stored at the customer’s facility behind the firewall so customers always know where the data is.