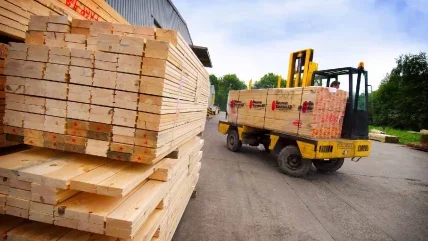
Value-added products in the wood-based panels industry have been very much in focus over recent years due to highly competitive markets on commodity items and a desire from panels customers for specific solutions.
In the OSB sector, we have seen an upward trajectory on higher performance requirements from OSB2 to OSB3 and an increased focus on OSB4 for some applications.
OSB4 has been around for over 20 years. Classed for heavy-duty load-bearing boards for use in humid conditions, the product is a denser, stronger and more water-resistant version of OSB3 for the most demanding applications.
The material is made by numerous mills globally in relatively small volumes, but capacity has been gradually increasing as markets, particularly in off-site construction, understand the improved performance benefits with relatively modest price premium over OSB3 or for product substitution over plywood.
Germany is the largest market for OSB4, with the product in common use within its construction sector.
Irish panels producer Medite SmartPly launched an OSB4 product in 2019, while Swiss Krono and Egger both report good and increasing demand for their OSB4 products. In Italy, I-Pan is standing out from the crowd with a poplar-based OSB4 product.
Magnumboard Increasing Popularity
Swiss Krono was the first panel producer to receive a German Technical Approval for OSB4 glued with formaldehyde-free binders, back in 2000 for its Polish Production.
These days OSB4 is only produced at its Heiligengrabe mill in Germany.
Stefan Gottfried, Swiss Krono wood construction engineer and application technology / product manager, said most of its OSB4 capacity was sold in Germany, with the product supplied into the normal housebuilding market seeing a steady level of demand.
“But because of increasing capacity of MagnumBoard, the volume of OSB4 will be more,” Mr Gottfried told WBPI.
Swiss Krono’s patented MagnumBoard system, which may only be produced by authorised licensees, are made from 25mm thick OSB4 boards measuring up to 18m x 2.8m.
Licensees glue together between three and ten plies of OSB4 boards and then shape them into bespoke wall, ceiling or roof sections. Advantages include elements with jointless sanded OSB surfaces, high density, fast and easy assembly and a minimal tendency to shrink or swell.
Swiss Krono’s OSB4 boards feature a characteristic raw density of more than 600kg/m3.
The company says this single-skin solid construction is also superior to traditional timber frame construction and avoids problematic aspects such as transitions between different materials, entrapped moisture and long construction times.
Swiss Krono has 15 MagnumBoard partners who work with the material, working on construction projects. They also support and advise architects, owner-builders, and other interested parties in everything from planning to assembly of these solid timber construction elements all the way to turnkey buildings.
These partners are in direct contact with the licensees, who prefabricate bespoke modules and/or panels to meet the construction partners’ specifications and supply them to the construction site.
MagnumBoard licensees are 3B TEC Holzbau GmbH, Ch. Borchard GmbH & Co. KG , Keilhofer GmbH, MMD – Magnumboard- Manufaktur-Deutschland, Henri VERMOT et Fils Sàrl (France) and WOOD & BUILD (Belgium).
Mr Gottfried said Swiss Krono’s volume of OSB4 for MagnumBoard has increased from about 4,000m3 to 6,000m3 in the last year.
“We are optimising our production line in Heiligengrabe to get a maximum OSB capacity of 600,000m³,” he said. “This will give us a capacity of 30,000m³ for OSB4 Magnumboard.”
He estimated the increased OSB4 Magnumboard capacity could be realized by the end of 2021/ into 2022.
“Two or three of our MagnumBoard licensees will increase capacity with new production lines. We already have a new licence partner who will start in 2021 and we are looking for more license partners.
“We started a new campaign to include Architects and to make MagnumBoard better known. The most increase in demand is multistorey residential buildings. This is a huge market for CLT, but also for MagnumBoard.
The benefits are the direct finishing of the inside surfaces of the walls and no swelling or shrinking.”
Egger OSB4 Top
We also contacted global producer Egger about its OSB4 production – its OSB 4 TOP is produced in the Wismar plant in northern Germany.
“We have observed an increasing demand there over the past years, especially due to the rising acceptance of timber construction,” said Egger.
“In German-speaking countries we supply approximately 40% of the OSB quantities for building with wood in the form of OSB 4 TOP.”
Egger said a large proportion of the OSB boards produced today are found in application areas with short usage periods and have low quality requirements, such as for the use of packaging. “However, these boards are also widely used in wood construction,” it said.
“Here, the differences become evident, as the higher demands on the performance of OSB boards are placed over a long period of time. In order to be able to execute these construction projects durably, materials with perfectly matched properties are therefore required.”
Egger has noticed a positive development for many years as quality prevails and the subject of safety becomes more and more important.
“Products such as OSB 4 TOP are indispensable for high-quality wood construction and customers in the German, Austrian and Swiss markets are also aware of this,” it said.
“More and more customers in other countries such as Czech Republic, Slovenia and Hungary rely on the product in order to be able to meet the relevant quality standards.”
Egger said when used as a load-bearing component in wall, roof and ceiling constructions, OSB 4 TOP is used as a single product to meet the requirements for constructions with regard to stiffness, vapour-barrier, and air tightness. The important physical property of air tightness, which is not regulated by the OSB manufacturing standard EN300, is confirmed by Egger as a guaranteed feature of its board on the basis of appropriate tests in the CE Declaration of Performance.
A special feature is production in a maximum format of 11.50m × 2.80m for prefabricated ceiling elements. Due to the product’s high compression core layer, the OSB 4 TOP board can be manufactured with a stable and highly durable tongue and groove profile designed to withstand the harsh building site conditions.
Thanks to its higher load-bearing capacity in structural flooring applications compared with particleboards or OSB3, the thickness of OSB4 can be reduced by 3-5 mm or alternatively span widths can be increased.
OSB 4 TOP board can also be processed as a stable dry screed. It is possible to lay it directly on impact- noise insulation or on wooden substructure.
Swiss Krono says a board thickness of 30mm can provide a fire resistance of more than 30 minutes, while the light and closed surface of the OSB 4 TOP tongue and groove board combined with a coating can form an attractive floor area in living and utility rooms.
Siempelkamp Line Gives Ultima Capacity
Irish producer MEDITE SMARTPLY launched its new ULTIMA OSB/4 in 2019 after significant investment in its OSB plant.
“When we researched OSB/4 products in the past we found low awareness among customers and specifiers, limited availability and variable quality”, said David Murray, Head of Technical Affairs and Ireland Sales Manager at MEDITE SMARTPLY.
“But we saw the potential for a stronger, heavier duty and more durable OSB panel in several market segments. Britain and Ireland are leading the way in offsite construction, both low and medium-rise timber and steel frame systems, and ULTIMA solves many design challenges in this sector”, he said.
This is a combination of customers upgrading from OSB/3 to OSB/4 and also replacing chipboard and plywood. “It is an opportunity to substitute imported and often inferior quality plywood with a high quality home-grown product. Specifiers are becoming increasingly aware that there is no such thing any more as ‘WPB’ plywood since the old BS 6566 standard was withdrawn almost a quarter of a century ago to make way for modern European Standards covering a wide range of wood panels.”
As a result, MEDITE SMARTPLY is steadily producing more of its MAX OSB/3 and ULTIMA OSB/4 products.
“We are getting an awful lot of technical enquiries for ULTIMA but they take time to work their way through the specification network.”
Unlike plywood, ULTIMA is made with zero-added formaldehyde resin and can be made in large formats up to 2.8m wide by 7.5m long and to a maximum thickness of 40mm, which opens up a whole new world of structural applications that plywood panels are limited by their 1.2m x 2.4m size.
ULTIMA has a higher density than plywood and is promoted as 30-35% stronger than OSB/3, while also being 20% more moisture resistant with a swelling in thickness after 24hrs immersed in water (EN317) of 12%, compared to 15% for OSB/3.
This additional technical performance is down to the company’s increased timber engineering capability afforded by the €60 million investment in the SMARTPLY plant.
The company purchased the latest generation of Siempelkamp ContiRoll pressing technology with intelligent process control using Prod-IQ.
“That’s the beauty of the continuous press. Every product has its own recipe (wood species, density, resin, wax, etc) and it’s quick to change from one product to the next and the difference in quality is incredible. We bought the highest spec continuous press line so we could respond quickly to a rapidly evolving offsite construction sector across our European market territories”.
Mr Murray said the extra performance of ULTIMA OSB/4 over MAX OSB/3 does not come with a big price premium, making specification easier for clients to justify.
“As the offsite construction market grows, we find ourselves making ULTIMA on a more regular basis.”
Market applications for ULTIMA include offsite construction systems, panelised systems, commercial buildings (insulated panels), industrial buildings (mezzanine flooring), site-based construction (Insulated Concrete Formwork), engineered timber components (long spanning cassettes), industrial packaging, decorative applications, and much more.
“Offsite construction floor, roof and wall cassettes are major applications for ULTIMA thanks to the higher strength, enhanced moisture durability and large panel sizes available which enables whole sections of buildings to be weatherproofed in a fraction of the time of traditional 8 by 4 foot panels”, said Mr Murray.
The online shopping explosion has created extra demand for storage space and companies see adding a mezzanine flooring layer in warehousing and distribution operations as a quick, effective solution, and ULTIMA STRONGDECK is particularly suited to this demanding application.
P5 particleboard commonly used in these applications is 38mm thick by 600mm wide by 2400mm long, whereas ULTIMA STRONGDECK is 30mm thick and 675mm x 2400mm. It is 17% lighter than P5 and because it is wider, requires less panels and installation is quicker.
18mm ULTIMA is also promoted to replaces 22mm P5 particleboard in normal housebuilding floor deck installations due to its high strength to thickness ratio.