It is little wonder that Loris Zanasi, managing director of Imal, was smiling broadly as we met in his San Damaso office. With the company’s sales reaching a new record for 2007/8 already, he seemed to have every reason to smile.
"We have had a very good order intake of EUR60m and are very satisfied with the business situation," said Mr Zanasi.
The Ligna exhibition this May also provided a boost to the company’s order book, with orders worth seven million euros taken at the show, he said.
The contract for a large gluing system for Kronospan’s 2,500m3/day particleboard mill in Jihlava, Czech Republic, was a major event of the show but other, less predictable, business was also done with customers who had not negotiated the deal beforehand.
Imal’s pallet block extrusion line chalked up three orders from Portugal, while a visitor previously unknown to Imal purchased laboratory equipment during the show.
May 2006 was also a significant date for the company as it was then that Imal and Pal came together in terms of ownership. The chief executive of Pal (located in Ponte di Piave), Romeo Paladin, sold his shares in his company to Imal shareholders and cemented an already close relationship between the two firms. They first exchanged a small percentage of each other’s shares in 1998 and removed areas of overlap in the two firms’ product ranges.
"The synergy of the two companies has increased since then," said Mr Zanasi. "In the last year, we have begun to have more technical meetings to exchange even more information than before and we have developed new ideas together which are still under development; utilising the mechanical expertise of Pal and the electrical/electronic expertise of Imal."
Stefano Benedetti, son of the family which founded Imal, has been part of this close cooperation. "For instance, we have developed a new type of OSB bunker – both green and dry bins – to avoid the breakage of flakes, without using picker, or doffing, rolls in front of the bins as these create a lot of fines and broken strands. We are aiming to increase the size of strands and reduce the amount of fines," he said.
"Another successful system we developed jointly is the new generation fibre resination system for MDF, to be installed after the dryer."
The latest installation of this system is at Alpha Wood’s MDF plant in Greece.
"With this system, we have achieved resin savings of 30 to 40%. It is the fourth generation and brings together over 10 years of experience. We have installed additional nozzles to inject the resin more evenly and changed the injection of warm air in different areas of the blender," explained Mr Benedetti.
A relatively recent product for Imal is the x-ray Press Security Device (PSD) to detect foreign bodies or glue lumps in a fibre mat before the continuous press to protect the press belts from damage. It also provides an accurate picture of the mat weight distribution, said Mr Benedetti.
Another brand new x-ray based system is the MDS100 on-the-line mat density scanner for the full width of the mat. "This will replace the traditional traversing scanner system," he asserted.
"We are also nearly ready with a completely new technology for blow detection which will be on the market this year," adds Mr Zanasi. "It will allow accurate readings and will require less maintenance than existing systems."
Upgrades for existing blow detection systems will also be offered.
An all-new version of the vertical density profile meter CDP600 is claimed to be very simple to install, with the x-ray transmitter and receiver both below the board. "This makes it cheaper and easier to install and enables the measuring of thin board with improved accuracy," said Mr Benedetti.
Some of Imal’s products are already well-established worldwide, like the mat damping spray which has clocked up over 100 units sold since its launch in 2002.
Another is the company’s gluing system, of which it has supplied over 280 since January 1994. An additional 14 units are due to be shipped to customers this year.
The above represents just part of the Imal scope of supply. Its moisture meters, employing both infra-red and microwave technology, and its range of laboratory quality control equipment add to the range.
"We are covering the majority of panel mill projects worldwide. We work as an independent supplier in around 75% of cases, but also with the major complete line suppliers and there are new projects coming up as we speak," concluded Mr Zanasi confidently.
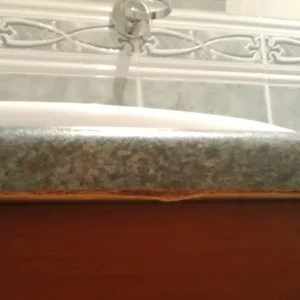