In a linked chain of events, plunging pulp chip prices have made possible increasing veneer raw material supplies for Potlatch, Inc in Oregon and Idaho.
The output of the company’s fast-growing hybrid poplar plantations has been favourably tested for veneer production, but some problems such as transportation distances have so far sidetracked that use.
The 17,000 acres of trees blanketing a flat semi-desert area of north central Oregon seemingly sprang up overnight, to the puzzlement of freeway drivers who buzz by. They’ve been managed as an agricultural crop since the first plantings in 1993.
“We’ll be producing 45 million board feet per year in sawlog volume and it’s all contiguous,predicted harvesting and marketing manager Pat Moore.
Regional hybrid poplar manager Greg Uhlorn explained the plantations’ origin: “We were concerned about our ability to supply chips for our pulp mill in Lewiston, Idaho.We looked at several alternatives and this looked like the best option. In 1993 we bought two large circle-irrigated farms and started converting them to drip irrigation for growing trees.We planted our first trees in 1994, looking for a six- or seven-year rotation for pulp chips.”
The growing environment on the planting site was good, lacking only water which was readily available from the large Columbia river five miles north. The potato farmers who formerly owned the land had developed circular pivoting irrigation systems.
The sandy soil is good. A freeway runs along one edge of the farm, a railroad mainline across it and there is that nearby Columbia river for barge transportation.
The problem was that the pulp chip market, in Mr Uhlorf’s words, “really turned on its ear after about the mid ’90s”. Today’s chip prices are less than half of what they were when the project started. This made the cost of producing the poplar chips uneconomical for pulp, and required rethinking the poplar management.
This prompted the decision to look at solid wood production and Potlatch began pruning to gain more clear wood which has a much higher value. They went from a seven-year to an 11-year cutting rotation and started planting just under 300 trees per acre, half the density of the pulpwood plantings. The utilisation target is hardwood lumber and plywood.
First prunings are restrained, only four or five feet, so as not to remove too many leaves which are important to growth. The trees are 10ft to 12ft high at the end of the first growing season. After two years they are 20ft to 30ft tall with pruning up to 9ft. Final pruning is 20 to 24ft and the fully-pruned trees will grow another five or six years before harvesting.
Potlatch is using traditional tree breeding, picking the best specimens, with no genetic work. It is looking for such things as fairly straight stems and branching perpendicular to the stems which will create smaller knots than angle-branching.
Most of the work is contracted including tree improvement in nurseries, cutting production for tree starts, logging and hauling. Plantings are entirely from cuttings roughly 13in long, 1/2in at the small end and 5/8in at the large end. Planters slip the cuttings into the prepared planting bed, in rows, with the top bud at ground level. Rows are 10ft apart and cuttings placed every 15ft.
The 3/4in plastic drip irrigation hose is laid down beside the cuttings with computer controlled irrigation starting in April, when the trees leaf out, and continuing until they start shutting down in September and October. Only eight inches or less of rain falls during the growing season. In the first year the new trees receive 6in to 10in of irrigation water, but older trees receive 40in to 42in.
Chemicals and fertiliser are injected into the water to combat tree diseases and insects and to speed growth. Weed killers limit vegetation harbouring animals and birds that can cause damage.
When Potlatch set up its farm it replaced the irrigation circle centre pivots with valve manifolds. It used as much of the existing buried pipe as possible, burying some additional PVC lines to supply the drip tubes.
The figures for the system are impressive. Pump capacity is 178,640 gallons per minute. There are 370 miles of buried pipe, from the 72in pipe under the freeway to the 11/2in pipe supplying the drip tubes. There are 14,300 miles of plastic drip tubing on the ground and 20 million emitters to supply water to about 7.4 million trees.
Mr Uhlorn said: “We’re looking at appearance-grade applications where structural strength is not critical. Our poplar is a good lightweight low density wood, light in colour. It machines, stains and paints well. This is the first hardwood plantation operation to be FSC certified.”
Harvesting units are blocks of 40 to 160 acres. Logging contractor Bryan Broadfoot uses a Timbco feller-buncher running a Quadco disc hot saw, moving across the field taking four rows at a time, cutting at ground level. He sorts as he goes, segregating trees which could produce solid wood. Earlier, when logging was only for pulp chips, he used a shear but this damages the butt log for solid wood production.
Another trailer-equipped Timbco picks up and hauls loads of 120 trees on a hayrack trailer to a roadside, returning with an empty one for the next load. These loads are entire trees, including limbs and leaves. A fifth wheel truck takes the trailers to a central processing site in the middle of the farm. Here, a Lako Oy dangler processor cuts solid wood logs to length. Because of the poplar’s natural crook and sweep, shorter bucking lengths dramatically increase utilisation.
There are two sorts for solid wood and the rest goes into a Peterson 5000 chain flail for chipping. The product is trucked to the port for barge shipment or directly to market.
Everything is utilised. Bark, limbs and tops are ground at the site in a Morbark tub grinder. Much of this is hauled back to the field as ground cover and nutrient base with the rest shipped to a nearby dairy in exchange for compost to apply to the fields. A Merry Crusher grinds up material on the logging blocks, preparing it for the next crop.
A Fuji King debarker will be on site soon, as the operation moves into full manufacturing. A 4ft lathe is a possibility. An option for enhancing the wood would be pressure-treating it with Indurite to increase hardness.
Mr Uhlorn said that at this point before the pruned material starts moving, veneer production would have to be dedicated to core inner ply. Later there will be opportunities for higher grades and face stock.
Jeld-Wen is incorporating the chips in its MDF doorskin production at White Swan, Washington. Mr Uhlorn believes the poplar would be good OSB material. Potlatch has run trials in its Minnesota OSB mills. Sawlogs go to Kinzua Resources sawmill at Pilot Rock, Oregon.
Mr Moore lists some plusses for the operation: “Our inventory is kept on the stump; we have a year-round operation so we have even flow and accessibility of product and even flow for shipment; and we’re accessible to interstate highways.”
He advised a maximum of three days from the stump, chipper, or mill for best recovery.
The tree wagons are unloaded with a Wagner loader and are either set down directly in front of the chipper or onto a small deck with the solid wood logs segregated from chip logs. A Link-Belt loads the hog, mounted on a Ford truck.
Greg Cooperrider, Potlatch’s plywood plant manager at St Maries, Idaho is enthusiastic about the material. He peeled eight truckloads of 7in to 10in, 17ft logs. “We conditioned them for 12 hours, but if they were fresh we could probably run them without conditioning,he said. One problem was the stringy, cedar-like bark.
He said it should be dried on a mild schedule to minimise splits and it requires slightly more glue than some other species.
Using 1/6in veneer, he laid it up into fiveply panels. “It would make a very nice substrate for overlays,he declared.
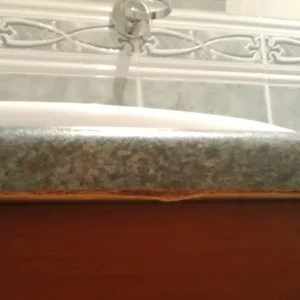